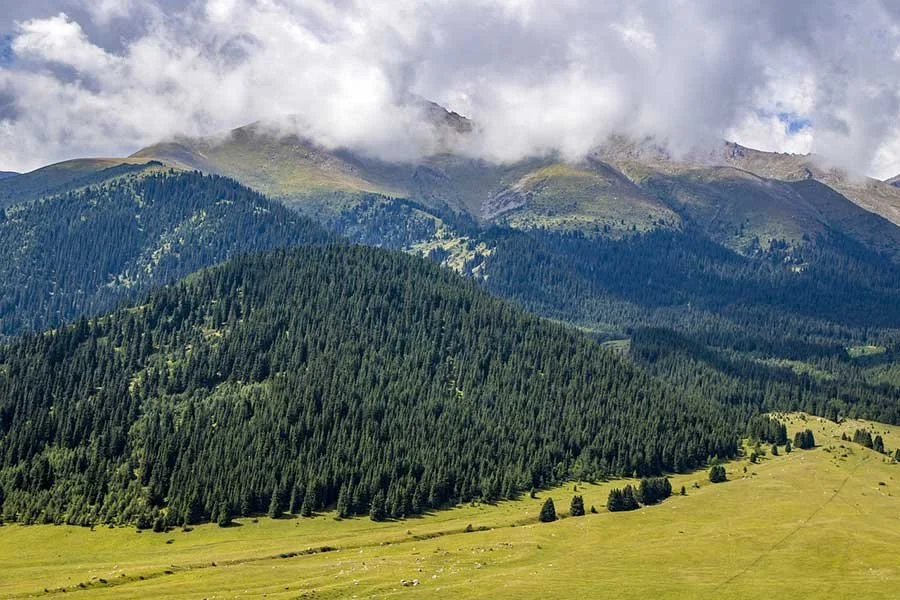
HSNO Requirements for the Timber Industry
Find out how the Hazardous Substances & New Organisms (HSNO) Act impacts the treated timber industry and ensures compliance with environmental and health standards.
**This page is currently being reviewed and new content will be added soon.* *
HSNO and the Timber Preservation Industry
This section provides essential information on the compliance requirements for the treated timber industry under the Hazardous Substances & New Organisms (HSNO) Act. The HSNO Act is a comprehensive piece of legislation in New Zealand designed to protect the environment and human health from the potential risks posed by hazardous substances and new organisms. It sets out the rules and regulations for managing and controlling the use, storage, transportation, and disposal of hazardous substances, such as chemicals used in timber treatment, as well as the introduction and management of new organisms.
Compliance with the HSNO Act is crucial for ensuring that the treated timber industry operates safely and responsibly, minimiSing risks to both people and the environment.
CCA Treatment Plants
Learn more about the legal obligations and safety requirements for CCA treatment plants under the HSNO Act, ensuring safe and compliant operations within the treated timber industry.
Location Test Certificates
Since CCA, ACQ, and CuAz treatment plants do not handle or use flammable substances, they are exempt from the requirement to obtain a Location Test Certificate. These certificates are typically needed to confirm that sites comply with safety standards for storing or using hazardous substances, but in this case, they are not necessary.
Approved Handler and Tracking Requirements
What This Means: CCA (Chromated Copper Arsenate) treatment chemicals are considered highly acutely toxic, meaning they can cause significant harm to health if not handled correctly. Because of their toxicity, the use of these chemicals is regulated under the HSNO Act.
Approved Handler Requirement: An "approved handler" is a person who has received specific training and certification to safely manage and use these hazardous substances. The law requires that an approved handler must be involved when these chemicals are used, but this does not mean that every individual handling the chemicals needs to be certified. Instead, an approved handler must be available on-site or accessible to guide and supervise others who are working with the chemicals, ensuring safe practices are followed.
Tracking Requirement: The tracking requirement mandates that the movement and usage of these toxic chemicals must be documented and monitored. This means that records must be kept detailing where the chemicals are stored, when and how they are used, and by whom. This tracking helps to prevent misuse, ensures safety procedures are followed, and provides a clear record in case of any incidents.
This regulation ensures that CCA chemicals are handled safely, minimising the risk to both people and the environment.
Stationary Container Systems
Stationary container systems with a capacity greater than 5000 litres require certification. A test certifier, approved for stationary tanks, must assess these systems.
Key compliance requirements include:
Tank design, construction, and installation pressure
Emergency pressure management
Level indicator requirements
Firefighting systems
Signage and record-keeping
Refer to Schedule 8 of the NZ Gazette Hazardous Substances (Dangerous Goods and Scheduled Toxic Substances) Transfer Notice 2004 for more detailed information.
Secondary Containment
Secondary containment measures, such as bunded areas, are essential to manage substances that may leak, spill, or spray from their primary containers. Compliance with the Hazardous Substances (Emergency Management) Regulations 2001 is required where applicable.
LOSP Treatment Plants
Discover the specific legal requirements for LOSP treatment plants under the HSNO Act, designed to protect workers and the environment while maintaining compliance in timber treatment processes.
Location Test Certificates
A Location Test Certificate confirms that a site complies with safety standards for storing or using hazardous substances. LOSPs typically have a hazard classification of 3.1C, requiring a Location Test Certificate for sites storing over 50,000 litres of these substances. Extensions may be granted by the Authority upon approval of an implementation plan.
Approved Handler and Tracking Requirements
What This Means: LOSP (Light Organic Solvent Preservative) chemicals can vary in their level of toxicity, which determines the level of regulation they are subject to. While not all LOSP chemicals require strict control, some are classified as highly acutely toxic (under classifications 6.1A, 6.1B, or 6.1C). These classifications indicate that the chemicals can cause serious health risks if mishandled.
Approved Handler Requirement: For LOSP chemicals that fall under these high toxicity classifications, an "approved handler" must be involved in their management. An approved handler is someone who has undergone specialised training and certification to safely handle hazardous substances. Although not every individual working with these chemicals needs to be certified, an approved handler must be available to supervise and guide the handling process to ensure safety protocols are followed.
Tracking Requirement: The tracking of highly toxic LOSP chemicals is mandatory. This means that detailed records must be kept on the storage, use, and movement of these substances. Tracking ensures that the chemicals are handled safely, minimises the risk of misuse, and provides a clear trail of documentation in case of any incidents or safety breaches.
This regulation is vital to maintaining a safe working environment and protecting both workers and the surrounding community from the potential dangers posed by highly toxic LOSP chemicals.
Stationary Container Systems
Stationary container systems with a capacity greater than 5000 litres require certification. A test certifier must assess these systems.
Compliance requirements include:
Tank design, construction, and installation pressure
Emergency pressure management
Level indicator requirements
Firefighting systems
Signage and record-keeping
Refer to Schedule 8 of the NZ Gazette Hazardous Substances (Dangerous Goods and Scheduled Toxic Substances) Transfer Notice 2004 for more detailed information.
Secondary Containment
Secondary containment systems, such as bunded areas, are required to manage potential leaks, spills, or sprays from primary containers. Compliance with the Hazardous Substances (Emergency Management) Regulations 2001 is mandatory.
Become a WOODmark® Licensee
NZTPC welcomes new WOODmark® licensees and is dedicated to supporting and nurturing the community.